Table of Contents
Quality inspection plays a crucial role in maintaining customer satisfaction and upholding your brand’s reputation. In this guide, we’ll delve into the essential steps and strategies to effectively deal with quality inspections for imported artificial plants for wholesale.
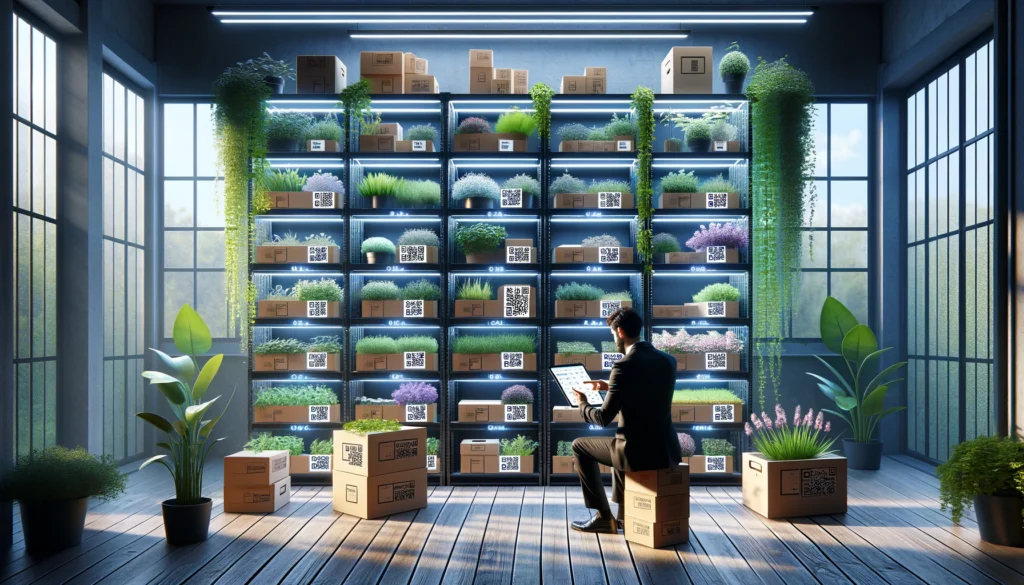
1. Understand Quality Standards:
In the dynamic world of artificial plants manufacturing, quality standards serve as the compass guiding product excellence and consumer satisfaction. Before embarking on the intricate journey of quality inspection, it’s imperative to immerse oneself in the realm of industry norms and regulations that govern artificial plants.
Firstly, delve into the intricacies of the materials employed in artificial plant production. From lush foliage to sturdy stems, each component contributes to the overall aesthetic appeal and longevity of the product. Familiarize yourself with the diverse array of materials available, ranging from high-quality plastics to lifelike silk fabrics. Understanding the properties and characteristics of these materials empowers you to discern between superior craftsmanship and subpar alternatives.
Next, unravel the mysteries of construction techniques employed in crafting artificial plants. From meticulous handcrafting to precision-driven machinery, the artistry behind each creation influences its durability and authenticity. Delve into the nuances of assembly methods, such as wire framing, injection molding, and hand-sculpting, to gain insight into the craftsmanship behind every botanical masterpiece.
Moreover, acquaint yourself with the durability expectations inherent in artificial plant manufacturing. Whether destined for indoor décor or outdoor landscaping, artificial plants must withstand the test of time and environmental elements. Explore industry standards related to UV resistance, water resistance, and flame retardancy to ensure compliance with regulatory requirements and customer expectations.
By immersing yourself in the rich tapestry of quality benchmarks, you pave the path towards informed decision-making and effective communication with suppliers and inspectors. Armed with a comprehensive understanding of quality standards, you can articulate your expectations with clarity and precision, fostering a collaborative partnership dedicated to delivering excellence in every leaf and petal.
2. Select Reliable Suppliers:
In the intricate web of global commerce, the quest for quality begins with the selection of reliable suppliers. Your journey towards ensuring superior artificial plants for wholesale hinges on partnering with manufacturers who embody a commitment to excellence. Here’s how to discern the gems from the rubble when scouting for dependable suppliers:
Firstly, embark on a voyage of thorough research to unearth manufacturers with a sterling reputation for producing top-tier artificial plants. Dive deep into industry forums, trade publications, and online platforms to glean insights into the market landscape. Seek out testimonials and reviews from fellow distributors and retailers to gauge the satisfaction levels and reliability of potential suppliers.
Next, don your detective hat and request samples from prospective suppliers to scrutinize their craftsmanship firsthand. Pay meticulous attention to detail, examining the quality of materials, precision of construction, and lifelike aesthetics of the artificial plants. By subjecting samples to rigorous scrutiny, you can discern between suppliers who prioritize quality and those who cut corners.
Furthermore, engage in a candid dialogue with potential suppliers to delve into the intricacies of their quality control processes. Inquire about their adherence to industry standards, certification protocols, and rigorous testing procedures. A transparent and forthcoming approach to quality assurance signals a supplier’s dedication to upholding the highest standards of craftsmanship and reliability.

Establishing strong relationships with reliable suppliers transcends mere transactional exchanges; it embodies a symbiotic partnership built on trust and mutual respect. Cultivate open lines of communication, foster collaborative problem-solving, and nurture a shared commitment to continuous improvement. By forging strong bonds with trusted suppliers, you lay the foundation for a seamless supply chain characterized by consistency, reliability, and unparalleled quality.
In the labyrinth of global sourcing, the quest for quality is not merely a pursuit; it’s a sacred covenant between supplier and distributor, united in the pursuit of excellence. Choose your partners wisely, for in their hands lies the power to shape the narrative of your brand and the satisfaction of your customers.
3. Specify Inspection Criteria:
The cornerstone of effective quality control lies in the meticulous specification of inspection criteria— the blueprint that delineates the path towards product excellence and customer satisfaction.
Begin by crafting a comprehensive dossier of quality standards that encapsulate the essence of your brand’s identity and customer expectations. Delve into the minutiae of product attributes, from the verdant hues of foliage to the sturdy resilience of stems, with a clarity that mirrors the brilliance of a crystal-clear stream. Define the parameters of color accuracy with precision, ensuring that each leaf exudes a chromatic allure that captivates the eye and stirs the soul.
Next, fortify the foundation of your inspection criteria with a steadfast commitment to structural integrity. Assess the robustness of each component with a discerning eye, scrutinizing the welds, joints, and connections with unwavering precision. Ensure that every stem stands tall with unwavering resilience, embodying a steadfast resolve to withstand the test of time with unwavering grace and poise.
Embrace the quest for lifelike realism with an unyielding fervor that knows no bounds. Evaluate the authenticity of botanical features with a discerning gaze, scrutinizing the texture, shape, and arrangement of leaves with unwavering scrutiny. Seek out the subtle nuances that breathe life into each petal, infusing the artificial landscape with an ethereal allure that transcends the boundaries of reality.
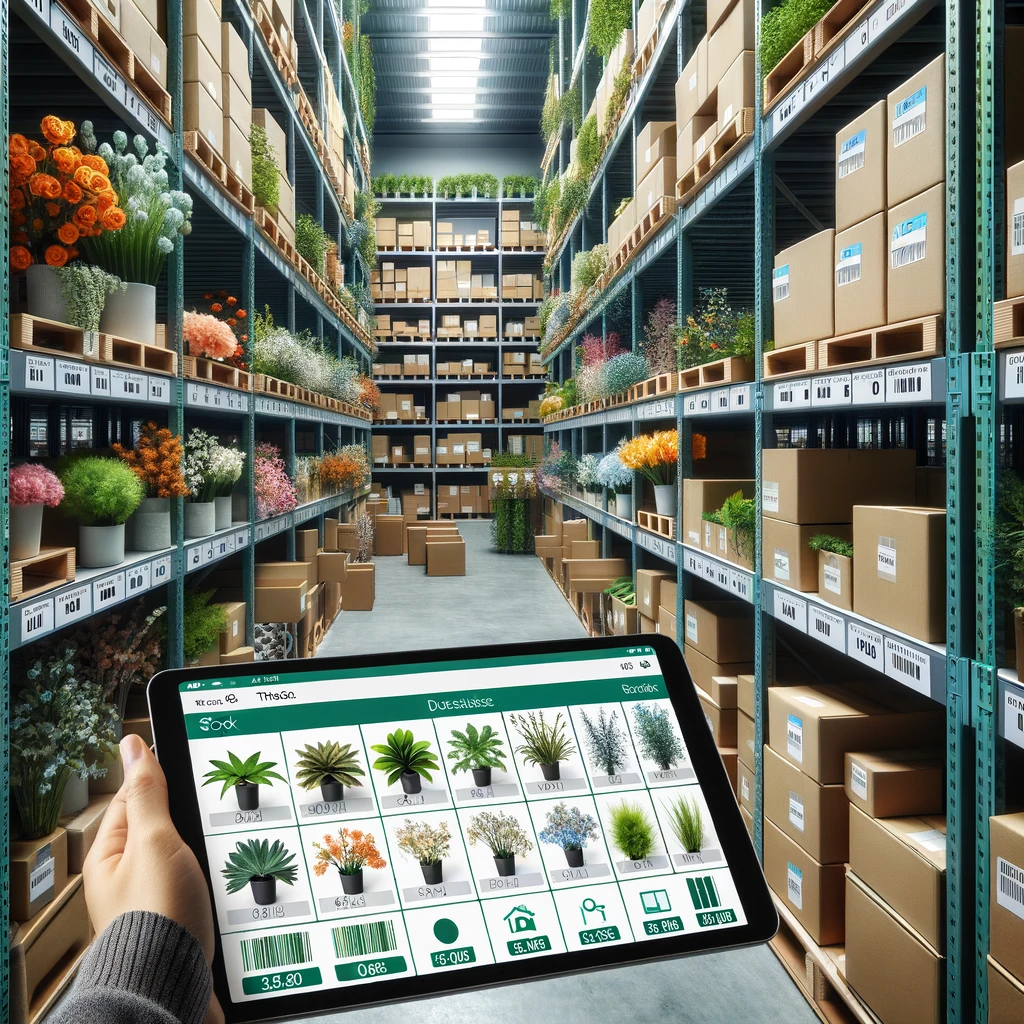
Furthermore, fortify the fortress of your inspection criteria with stringent packaging requirements that shield your products from the perils of transit. Specify the materials, dimensions, and protective measures with a clarity that leaves no room for interpretation, ensuring that each shipment arrives unscathed and pristine in its journey from factory to doorstep.
By providing specific guidelines to both suppliers and inspection agencies, you forge a shared understanding that transcends language barriers and cultural divides. Minimize ambiguity, maximize alignment, and cultivate a culture of excellence that permeates every facet of your supply chain. With a steadfast commitment to clarity and precision, you pave the path towards a future where quality reigns supreme, and customer satisfaction knows no bounds.
4. Pre-shipment Inspection:
Implementing robust pre-shipment inspections serves as a bulwark against the perils of defects and discrepancies, safeguarding the integrity of your brand and the satisfaction of your customers.
Firstly, enlist the expertise of accredited third-party inspection agencies or deploy in-house quality control teams to spearhead the inspection process. Whether entrusting the task to external specialists or nurturing an in-house cadre of inspectors, the goal remains steadfast: to conduct comprehensive assessments that leave no room for error.
Embrace a holistic approach to inspections that traverses the entire spectrum of product attributes, from the visual allure of the foliage to the functional prowess of the stems. Evaluate the color accuracy, texture, and lifelike appearance of the artificial plants with an eagle-eyed precision that mirrors the discerning gaze of your customers. Probe beneath the surface to assess structural integrity, ensuring that each leaf and petal withstands the test of time with unwavering resilience.
Furthermore, scrutinize the packaging with meticulous attention to detail, ensuring that each shipment is fortified against the rigors of transit. Assess the adequacy of protective measures, such as cushioning materials and secure fastenings, to minimize the risk of damage during transportation. By fortifying the packaging fortress, you fortify the sanctity of your products and the satisfaction of your customers.
Leverage the power of technology to augment the inspection process with digital tools and analytics that elevate precision and efficiency. Embrace digital imaging, spectroscopy, and machine learning algorithms to unravel the intricacies of product quality with unrivaled accuracy and speed. By harnessing the synergies of human expertise and technological innovation, you forge a formidable alliance against the specter of defects and deviations.
In the realm of pre-shipment inspections, vigilance is the watchword, and thoroughness is the mantra. Leave no leaf unturned, no stem unchecked, as you embark on a quest for perfection that transcends borders and boundaries. By embracing the rigors of scrutiny with unwavering resolve, you pave the path towards a future where quality reigns supreme, and customer satisfaction knows no bounds.
5. Document Inspection Findings:
As guardians of product integrity, it is paramount to keep meticulous records of inspection findings— a treasure trove of data that illuminates the path towards excellence and safeguards against the shadows of uncertainty.
Capture the essence of inspection findings through a symphony of mediums, from vivid photographs that immortalize each botanical detail to precise measurements that quantify the intricacies of product dimensions. Let every snapshot and figure serve as a testament to the unwavering commitment to quality that defines your brand.
Furthermore, weave a narrative of insight and analysis through written reports that distill the complexities of inspection findings into a coherent narrative. Chronicle the journey of scrutiny with meticulous attention to detail, articulating observations, concerns, and recommendations with clarity and precision. Let every word penned be a beacon guiding the ship through the fog of ambiguity towards the shores of resolution and corrective action.
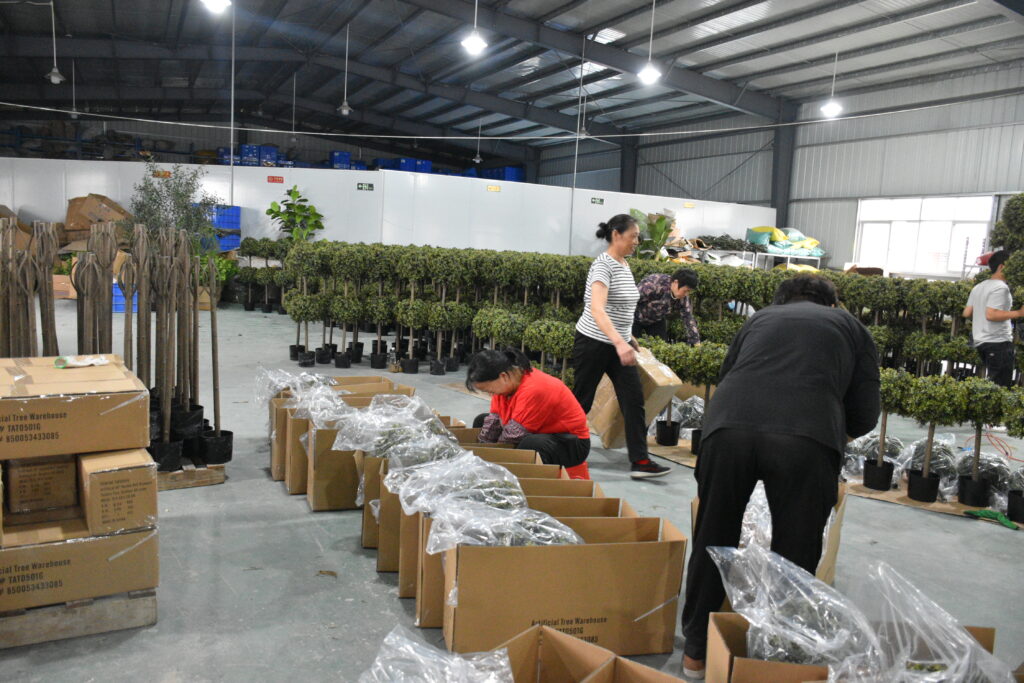
Embrace the power of documentation not merely as a bureaucratic chore, but as a strategic asset that fortifies the fortress of your supply chain against the perils of uncertainty and dispute. In the event of discrepancies or disputes, the comprehensive documentation serves as a bulwark of evidence, empowering stakeholders to navigate the labyrinth of resolution with confidence and clarity.
Moreover, leverage the insights gleaned from inspection findings to fuel a culture of continuous improvement that transcends boundaries and borders. Harness the power of data analytics to unearth patterns, trends, and opportunities for enhancement, propelling your brand towards ever greater heights of excellence and customer satisfaction.
In the realm of quality assurance, documentation is not merely a means to an end; it is a sacred covenant that binds together the threads of transparency, accountability, and integrity. Embrace its power, wield it with care, and let it serve as the cornerstone upon which your brand’s reputation and success are built.
6. Communicate with Suppliers:
First and foremost, lay the foundation for open communication by extending an olive branch of trust and goodwill to your suppliers. Foster a culture of transparency and collaboration that encourages candid dialogue and constructive feedback. Embrace the ethos of partnership, recognizing that success is not a zero-sum game but a collective journey towards shared prosperity.
Provide timely and actionable feedback to suppliers based on inspection reports and quality assessments. Approach the process with a spirit of collaboration rather than confrontation, framing feedback as an opportunity for mutual growth and improvement. Highlight areas of strength and opportunities for enhancement, fostering a culture of continuous learning and refinement.
Moreover, engage in proactive problem-solving by collaboratively identifying root causes and implementing corrective measures. Leverage the insights gleaned from inspection findings to inform strategic decision-making and drive process improvements. Encourage suppliers to embrace a mindset of continuous improvement, challenging the status quo and pushing the boundaries of excellence.
Embrace technology as an enabler of communication and collaboration, leveraging digital tools and platforms to streamline communication processes and facilitate real-time exchange of information. Embrace the power of data analytics to unearth actionable insights and drive informed decision-making. By harnessing the synergies of technology and human ingenuity, you can unlock new frontiers of collaboration and innovation.
7. Implement Quality Assurance Protocols:
By instilling a culture of vigilance and proactive monitoring, you can fortify the fortress of quality and ensure that each botanical masterpiece meets the lofty standards of your brand.
First, embark on a quest for transparency and accountability by conducting regular factory audits that offer a glimpse into the inner workings of your manufacturing partners. Embrace the ethos of diligence and thoroughness as you traverse the production floor, scrutinizing every facet of operations with an eagle-eyed precision. From raw material sourcing to production processes, delve deep into the intricacies of production to uncover potential areas of improvement and optimization.

Furthermore, integrate in-process inspections into the fabric of your manufacturing operations to nip potential issues in the bud before they have a chance to escalate. Implement a regimented schedule of inspections at key checkpoints along the production line, where trained inspectors assess the quality of workmanship and adherence to specifications. By intervening early in the production process, you can identify and rectify deviations from quality standards with speed and efficiency, preventing quality-related issues from proliferating downstream.
Embrace the element of surprise by incorporating random product testing into your quality assurance arsenal, where samples are selected at random from finished goods inventory and subjected to rigorous scrutiny. Embrace the ethos of randomness and unpredictability as you cast a wide net of scrutiny, ensuring that every product undergoes the same level of rigorous assessment. By instilling a culture of accountability and quality consciousness, you can foster a relentless commitment to excellence that permeates every facet of your organization.
Leverage the power of technology to augment your quality assurance efforts with digital tools and analytics that elevate precision and efficiency. Embrace the power of automation, artificial intelligence, and machine learning algorithms to uncover patterns, trends, and anomalies that may escape the human eye. By harnessing the synergies of human expertise and technological innovation, you can unlock new frontiers of quality assurance that propel your brand towards unparalleled heights of excellence and customer satisfaction.
In the dynamic landscape of modern commerce, the quest for quality is not merely a pursuit; it’s a sacred covenant that binds together suppliers, distributors, and customers in a shared journey towards excellence. By implementing robust quality assurance protocols that span the entire supply chain, you can fortify the fortress of quality and ensure that each product that bears your brand’s name embodies the essence of excellence and integrity.
8. Continuous Improvement and Feedback Mechanisms:
First and foremost, cast a wide net of inquiry, soliciting feedback from customers, suppliers, and inspection agencies with an insatiable thirst for insight and enlightenment. Embrace the ethos of humility and openness as you invite stakeholders to share their perspectives, experiences, and suggestions for improvement. From customer satisfaction surveys to supplier performance evaluations, harness the power of feedback data to illuminate the path towards enhancement and refinement.
Analyze feedback data with a discerning eye, mining insights and trends that offer glimpses into the intricacies of customer preferences, pain points, and expectations. Embrace the ethos of data-driven decision-making as you distill feedback data into actionable insights that inform strategic decision-making and drive continuous improvement initiatives. Identify recurring themes and patterns that emerge from the feedback data, pinpointing areas for enhancement and optimization that align with your brand’s vision and values.
Implement corrective measures with diligence and determination, translating feedback insights into tangible actions that elevate product quality and customer satisfaction. From fine-tuning product designs to optimizing manufacturing processes, embrace the spirit of innovation and adaptation as you embark on a journey of continual refinement. Engage stakeholders in the process of improvement, soliciting their input and collaboration to ensure that corrective measures are rooted in collective wisdom and shared commitment to excellence.

Moreover, foster a culture of accountability and ownership by establishing clear roles and responsibilities for implementing feedback-driven improvements. Empower employees at all levels of the organization to take ownership of the improvement process, fostering a sense of pride and ownership in the pursuit of excellence. Celebrate successes and milestones along the journey of continuous improvement, recognizing and rewarding individuals and teams for their contributions to product quality and customer satisfaction.
In conclusion, dealing with quality inspections for imported artificial plants requires careful planning, attention to detail, and effective communication. By following these guidelines and implementing robust quality assurance practices, you can uphold the highest standards of product quality and meet the expectations of your customers worldwide. Remember, quality is not just a goal; it’s a journey towards excellence.