In the bustling world of artificial plant distribution, maintaining high-quality standards is paramount. Your reputation hinges not only on the variety and aesthetics of your offerings but also on the consistency and reliability of your products. From production to delivery, every step in the process presents an opportunity to uphold quality control measures that set you apart in the market. In this guide, we’ll walk through essential strategies to ensure the excellence of your artificial plant inventory every step of the way.
1. Selecting Reliable Suppliers:
The foundation of quality control starts with choosing reputable suppliers. In the competitive landscape of artificial plant business, the integrity of your supply chain directly impacts the quality of your products and, consequently, your brand reputation. Look beyond mere affordability and consider manufacturers who prioritize quality materials, impeccable craftsmanship, and environmental sustainability. Seek out suppliers who share your commitment to producing ethically sourced and environmentally friendly products.
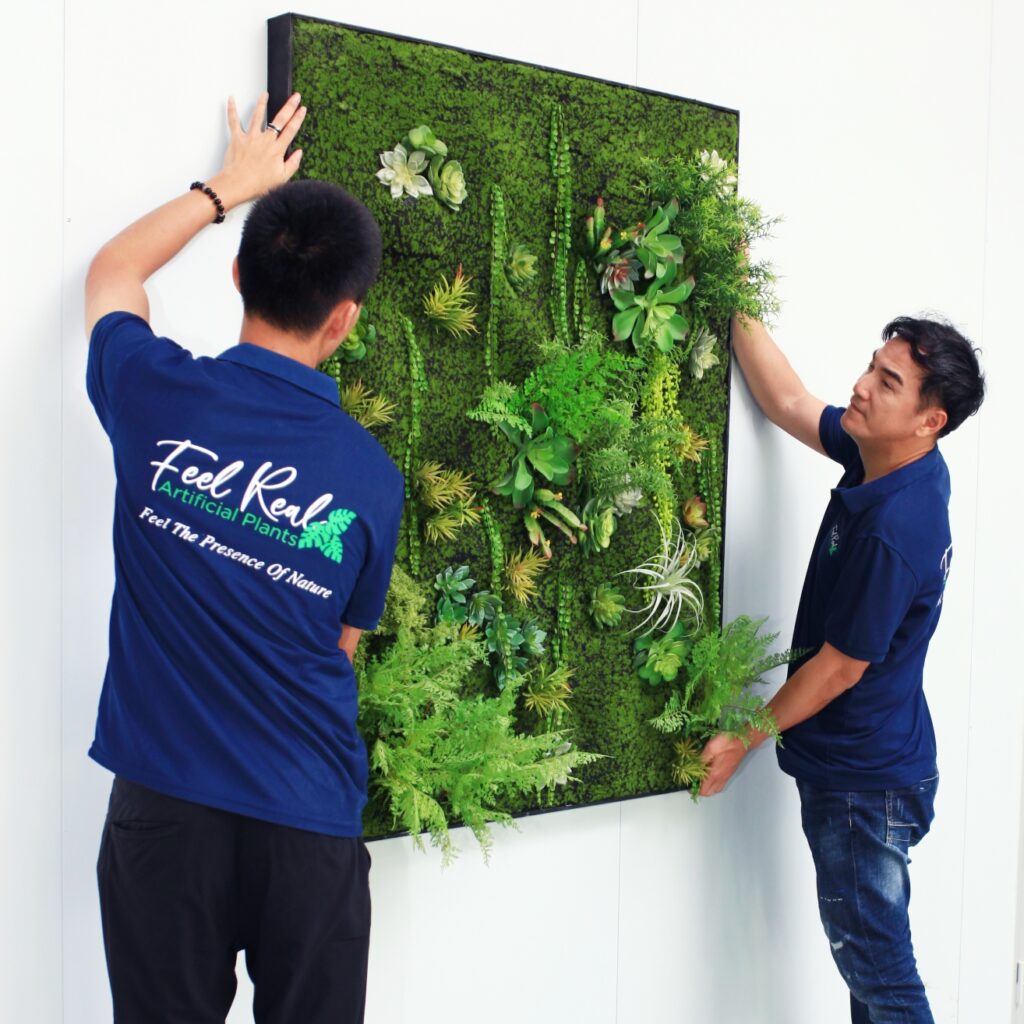
Conduct thorough research before engaging with potential suppliers. Investigate their track record, certifications, and industry reputation. Are they known for consistently delivering high-quality products? Do they adhere to ethical labor practices and environmental regulations? Request samples of their products to assess their quality firsthand. Inspect the materials used, the attention to detail in craftsmanship, and the overall aesthetic appeal.
Establish clear communication channels with your prospective suppliers from the outset. Open and transparent communication is essential for building trust and resolving any issues that may arise throughout the partnership. Clearly communicate your expectations regarding quality standards, delivery schedules, and pricing agreements. Address any concerns or questions promptly to ensure alignment and avoid misunderstandings down the line.
2. Implementing Rigorous Material Inspection:
The quality of artificial plants is intrinsically linked to the materials used in their construction. Implementing rigorous material inspection protocols is essential to ensuring the excellence of your products and safeguarding the trust of your customers.
Prioritize thorough material inspections to verify compliance with safety regulations and quality standards. Test each component for durability, ensuring that it can withstand the rigors of handling, shipping, and display. Assess colorfastness to prevent fading or discoloration over time, especially when exposed to sunlight or other environmental factors. Evaluate resistance to moisture to prevent mold or deterioration, particularly in humid environments.

Incorporate testing for resistance to environmental factors such as UV radiation, temperature fluctuations, and humidity. Artificial plants may be used in a variety of settings, from indoor spaces to outdoor gardens, so it’s crucial to ensure their resilience in different conditions.
3. Enforcing Stringent Production Standards:
Maintaining quality during the production process requires unwavering commitment to adherence to stringent protocols and procedures. Implementing robust quality control measures at every stage of production is paramount to ensuring that your artificial plant inventory meets the highest standards of excellence. From the procurement of raw materials to the final assembly of finished products, each step in the production chain must be meticulously monitored and evaluated.
Conduct regular audits and inspections to identify any deviations from established standards promptly. By employing advanced quality control techniques, such as statistical process control and failure mode and effects analysis, you can pinpoint potential issues before they escalate into significant problems. Foster a culture of quality consciousness among production staff, emphasizing the importance of precision, accuracy, and attention to detail in every task they undertake.

Effective communication channels between different departments are essential to facilitate seamless coordination and collaboration. Encourage cross-functional teams to work together to identify areas for improvement and implement corrective actions proactively. Invest in training and development programs to enhance the skills and competencies of the production workforce, empowering them to uphold the highest standards of quality in their work.
4. Craftsmanship and Attention to Detail:
Artificial plants are more than just products; they are meticulously crafted works of art that replicate the beauty of nature. As guardians of this artistry, it is incumbent upon you to maintain an unwavering commitment to craftsmanship and attention to detail throughout the production process.
From the delicate veins of a leaf to the subtle nuances of color and texture, every element of your artificial plants should reflect a dedication to excellence. Encourage your suppliers to take pride in their workmanship, infusing each piece with passion and creativity. Provide them with the tools, training, and resources they need to unleash their full potential and bring your vision to life.
Emphasize the importance of authenticity and consistency in your product range. Whether you specialize in tropical foliage, desert succulents, or flowering blooms, ensure that each design reflects the unique characteristics of its real-life counterpart.
5. Comprehensive Inspection Protocols:
Before any shipment enters your inventory, it’s imperative to conduct comprehensive inspections to uphold the quality standards of your artificial plant offerings. These inspections serve as the final line of defense against defects or inconsistencies that could compromise customer satisfaction.

Scrutinize each item for imperfections in color, shape, texture, and overall construction. Develop standardized inspection protocols that leave no room for oversight, ensuring that every aspect of the product meets your exacting standards. Ask your suppliers to execute these protocols with meticulous attention to detail, emphasizing the importance of consistency and accuracy in their assessments.
Utilize a variety of quality control tools to enhance the effectiveness of your inspection processes. Implement checklists to ensure that all relevant criteria are evaluated systematically. Employ sampling techniques to assess representative samples from each batch, providing insights into the overall quality of the shipment. Invest in state-of-the-art inspection equipment, such as magnification devices and colorimeters, to facilitate precise measurements and analysis.
6. Effective Packaging Practices:
Proper packaging is not merely a logistical consideration; it’s a critical aspect of preserving the integrity of your products throughout the shipping and storage process. Invest in high-quality packaging materials that provide robust protection against the rigors of transportation and storage.
Select durable materials that offer adequate cushioning to minimize the risk of damage during transit. Foam inserts, bubble wrap, and air pillows can help absorb shocks and vibrations, preventing breakage or deformation of delicate components. Choose packaging solutions that are resistant to moisture, sunlight, and other environmental factors, safeguarding your products from degradation over time.
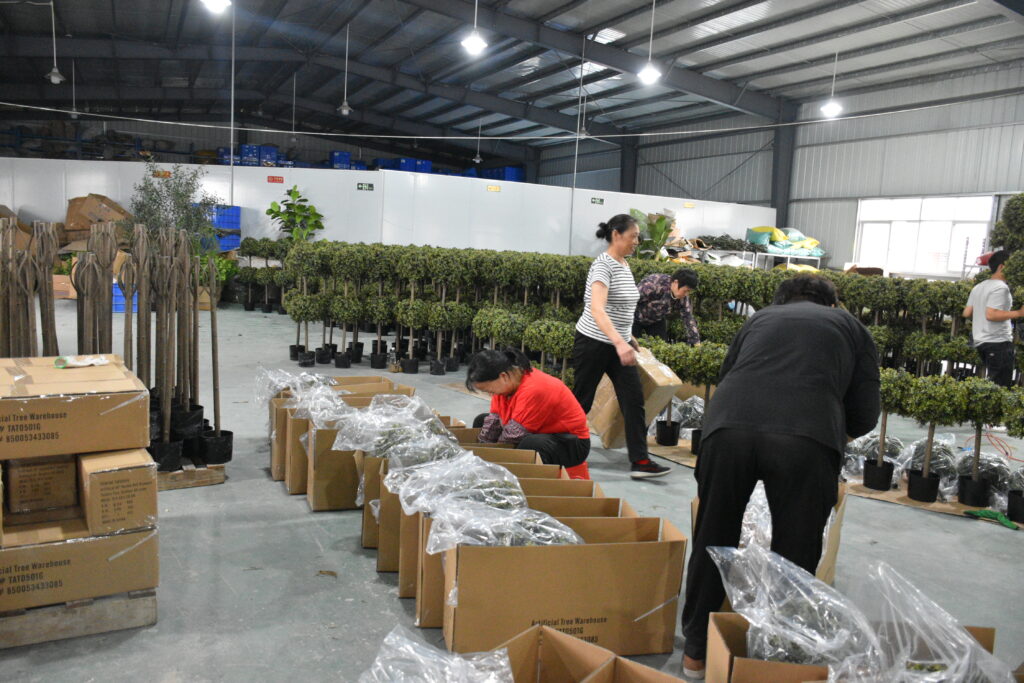
Clearly label packages with handling instructions and product information to ensure proper care and handling throughout the supply chain. Include details such as assembly instructions, material composition, and product specifications to facilitate a smooth customer experience upon receipt. Consider incorporating eco-friendly packaging options to align with your commitment to sustainability and environmental responsibility.
7. Streamlined Distribution Processes:
Efficiency lies at the heart of successful distribution operations, ensuring timely deliveries and ultimately driving customer satisfaction. To achieve this, it’s essential to streamline your distribution processes, optimizing them to minimize handling and transit times while maximizing the integrity of your products.
Start by analyzing your current distribution channels and identifying areas for improvement. Are there bottlenecks or inefficiencies that could be addressed? Look for opportunities to automate repetitive tasks, such as order processing and inventory management, to free up valuable time and resources.
Collaborate with reliable logistics partners who share your commitment to quality and efficiency. Choose partners with a proven track record of on-time deliveries and minimal incidents of damage or loss. Establish clear communication channels to keep them informed and aligned throughout the shipping process.
Implement robust tracking mechanisms to monitor shipments in real-time and proactively address any issues that may arise. Utilize technologies such as GPS tracking and RFID tagging to maintain visibility and control over your inventory at every stage of the distribution chain.
8. Customer Feedback and Continuous Improvement:
In the dynamic world of artificial plant business, customer feedback is invaluable for driving continuous improvement and maintaining a competitive edge in the market. Actively solicit feedback from your customers to gain insights into their satisfaction levels, preferences, and pain points.
Deploy a variety of feedback collection methods, including customer surveys, reviews, and direct communication channels, to gather comprehensive insights into the customer experience. Encourage honest and constructive feedback, making it easy for customers to share their thoughts and opinions.

Analyze the feedback collected systematically, identifying recurring themes and areas for improvement. Pay close attention to any issues or concerns raised by customers, addressing them promptly and proactively. Use this feedback to inform your quality control processes, driving continuous improvement and innovation in your product offerings.
Engage with customers transparently, keeping them informed of any changes or improvements implemented as a result of their feedback. This demonstrates your commitment to customer satisfaction and fosters trust and loyalty over time.
By implementing these strategies, you can establish yourself as a trusted provider of high-quality artificial plants in the market. Consistency, reliability, and attention to detail will not only earn you repeat business from satisfied customers but also solidify your reputation as a leader in the industry.
Remember, quality control is not just a one-time effort but an ongoing commitment to excellence at every stage of the production and delivery process. Stay vigilant, stay proactive, and your artificial plant business will thrive in today’s competitive marketplace.